Digital Transformation in Manufacturing: What it Means and Why it Matters
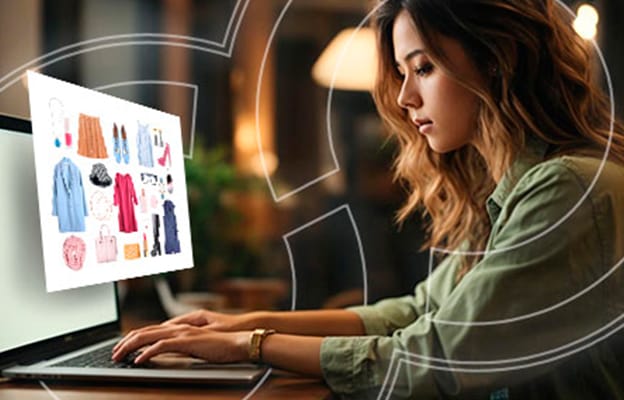
From smart factories to real-time data analysis, today’s forward-thinking manufacturers understand the need to integrate new digital technologies into their operations. In fact, research from IndustryWeek found that 86% of surveyed manufacturing professionals work for companies currently at some stage of digital transformation.
And while the benefits of digital transformation are clear, many companies face significant challenges in their journey. Budget constraints, security concerns, and workforce limitations can all hamper success in digital transformation.
In this article, we’ll break down the essentials of digital transformation in manufacturing, and offer a high-level roadmap for companies looking to better integrate emerging technologies into their workflows and product development processes.
What is Digital Transformation in Manufacturing?
Digital transformation involves leveraging digital technologies—such as AI, IoT (Internet of Things), and automation—to improve operations, drive efficiency, and create new and improved business models.
According to a recent industry report, the estimated market size of digital transformation efforts for manufacturers in 2024 was more than $367 billion—a number expected to increase to $876 billion by 2029.
This transformation can also include other digital concepts, such as digital twins, which describe creating and managing a physical workflow’s digital or virtual version and how they communicate. According to a 2024 report by the Manufacturers Alliance® Foundation, nearly 80% of manufacturers use digital twin concepts to improve product development and forecast changes and quality control issues.
Some of the most important aspects of digital transformation in manufacturing include:
- Data Analytics: Enables manufacturers to make data-driven decisions, improving responsiveness to market demands.
- Automation: Streamlines production processes, reduces human intervention and increases productivity.
- AI and Machine Learning: Enhances predictive maintenance, optimizes supply chains, and improves product quality.
- IoT (Internet of Things): Integrates connected devices and sensors for real-time monitoring and optimization of operations.
These technologies work together to create smarter manufacturing systems that respond dynamically to changes, improve efficiency, and enable manufacturers to stay competitive.
The Current State of Digital Transformation in Manufacturing
Although most manufacturers appear to be in some stage of digital transformation, there’s a wide gap between companies that have successfully matured with technologies and those that have not.
According to IndustryWeek, larger manufacturers may have an advantage: those with annual revenues between $500 million and $900 million are likely to be farther ahead in the transformation journey than those earning less than $500 million annually.
Still, even the smallest manufacturers can benefit from integrating more technologies into all aspects of the manufacturing process—and it’s never too late to start. A Recent PwC study found that only one-third of manufacturers who’ve started the transformation process are beyond their “initial” stages.
Some of the ways modern manufacturers can outline their transformation goals may be based on concepts or platforms like:
- Smart Factories: Integrated manufacturing systems use data to optimize real-time performance.
- Additive Manufacturing (3D Printing): Enables rapid prototyping and reduces waste.
- Digital Twins: Virtual models of physical processes allow for real-time monitoring and optimization.
- Sustainability Initiatives: Digital tools minimize energy consumption and waste, making manufacturing more sustainable.
These trends represent just a few of the ways manufacturers are leveraging digital technologies to transform their operations, in turn leading to some massive benefits across all types of business operations.
Benefits of Digital Transformation in Manufacturing
Digital transformation offers significant benefits to manufacturers, improving everything from operational efficiency to customer satisfaction. According to research by McKinsey, manufacturers that successfully implement digital transformation could see labor productivity increase by 15% to 30% and manufacturing downtime reduced by up to 50%.
Here are some of the main ways digital transformation can benefit manufacturers:
- Operational Efficiency: Predictive maintenance and automation reduce downtime and increase production speed, ensuring manufacturers can meet market demand quickly and efficiently.
- Cost Reduction: Manufacturers can cut costs by optimizing production schedules and reducing waste. According to McKinsey, digital transformation can reduce operational and product costs by 10% to 20% in many instances by improving areas of error and waste.
- Enhanced Product Quality: Real-time monitoring allows manufacturers to identify and resolve defects early in production, improving overall product quality.
- Improved Customer Satisfaction: Agile production systems allow manufacturers to respond quickly to customer needs and provide more customized products, enhancing the customer experience.
Sustainability: Digital tools help manufacturers track and optimize resource usage, reducing energy consumption and waste.
How to Digitally Transform Your Manufacturing Business
Successfully implementing digital transformation requires more than just adopting new technologies—it’s about aligning those technologies with your business goals. Here’s an overview of how to make digital transformation work for your company.
Initial Assessment
Begin by evaluating your current processes and identifying areas where digital tools can have the most significant impact. Focus on reducing downtime, improving supply chains, and enhancing customer service. Other benefits of transformation will often trickle down from these core priorities.
Digital Strategy Development
For better or worse, there are no “one size fits all” transformation strategies. Many manufacturers struggle with defining a clear business case for digital initiatives: the Manufacturers Alliance® Foundation found that over one-third of manufacturers cite budget constraints, security concerns, and labor shortages as challenges to their transformation goals.
When determining what technologies and platforms to integrate into your manufacturing processes, consider your core business goals and a realistic view of your current and future labor and machine resources. Setting specific goals and objectives will ensure your strategy is actionable, measurable, and attainable.
Technology and Platform Selection
With a wide array of technologies available, selecting those that will provide the greatest value is crucial. For example, manufacturers that adopt digital twin technology can improve real-time quality monitoring and reduce defects in a way that traditional simulation and forecasting can’t.
You can also consider holistic all-in-one platforms, like product lifecycle management (PLM) software, that manage complex workflows and processes on one “single source of truth.” When considering different technologies and platforms, it’s best to consider what tools can integrate with your current operations and structure.
Change Management
Change management is often cited as one of the most significant barriers to successful digital transformation. Cultural resistance and a lack of alignment between functions can slow down progress.
A significant number of manufacturers report challenges with integrating new systems and getting employees, teams, and outside vendors or suppliers to adopt new integrations and updated operating procedures.
Measuring Success & Iteration
Once digital tools are implemented, it’s important to measure their effectiveness. In their research, McKinsey claims that manufacturers can see productivity improvements of 15% to 30%, but measuring success through KPIs such as reduced machine downtime and improved throughput is essential—and different for each business.
To fully measure the success of your transformation efforts, it’s critical to know the KPIs and metrics that drive your business and are most likely to change—and improve—as you integrate more efficient technologies.
How PLM Can Streamline Digital Transformation for Manufacturers?
PLM tools and platforms can play a pivotal role in the digital transformation of manufacturing, especially for companies committed to long-term sustainability.
As manufacturers increasingly prioritize eco-friendly processes and products, PLM provides a centralized platform to manage every stage of the product lifecycle with transparency, efficiency, and sustainability in mind.
With the right approach to manufacturing PLM, companies can:
Streamline Product Development
PLM allows manufacturers to incorporate sustainability at every step of product development, from initial concept to final production.
By providing real-time access to material data, manufacturers can ensure that products are designed using sustainable materials, reducing waste and energy consumption. This transparency enables manufacturers to more easily meet regulatory requirements and align with eco-certifications.
Enable Circular Economy Strategies
PLM systems support the adoption of circular economy practices by facilitating better planning and design for product reuse, recycling, and remanufacturing.
With a complete view of a product’s lifecycle, manufacturers can identify opportunities to extend the life of products and reduce their environmental impact. This strategic approach helps companies minimize waste, reduce resource consumption, and optimize products for easier disassembly or material recovery.
Improve Supply Chain Visibility and Collaboration
Sustainable manufacturing requires a transparent and collaborative supply chain. PLM allows manufacturers to track materials and components sourced from multiple suppliers, ensuring they meet sustainability criteria.
This visibility into the supply chain enables better decision-making and enhances collaboration between departments and external partners, helping to identify the most environmentally friendly options.
Reduce Time-to-Market
In an industry where speed is crucial, PLM accelerates the time-to-market for sustainable products by automating workflows, improving collaboration, and reducing errors.
By digitizing the entire product development process, manufacturers can launch sustainable products faster while optimizing resources and reducing the carbon footprint of the manufacturing process.
Drive Continuous Innovation
As sustainability standards evolve, manufacturers must remain agile and continuously innovate. PLM supports ongoing product improvements by enabling easy access to historical product data, performance analytics, and feedback loops. This ability to innovate efficiently allows manufacturers to remain competitive while meeting new sustainability challenges.
By integrating PLM into their digital transformation journey, manufacturers gain a competitive edge and ensure that sustainability is embedded at the core of their operations, enabling them to lead the way in responsible manufacturing.
Transform Your Tech, While Transforming Your Business
Digital transformation is reshaping the manufacturing industry, offering opportunities to increase efficiency, reduce costs, and improve product quality. Manufacturers that fully embrace digital tools will gain a competitive advantage, while those that hesitate risk being left behind.
At Centric Software, we help manufacturers streamline their operations and embrace digital transformation. Request a demo today to learn how our product lifecycle management (PLM) solutions can support your digital journey and maximize your business’s potential.