Supply Chain Disruption: How to Build Resilience in Product Development
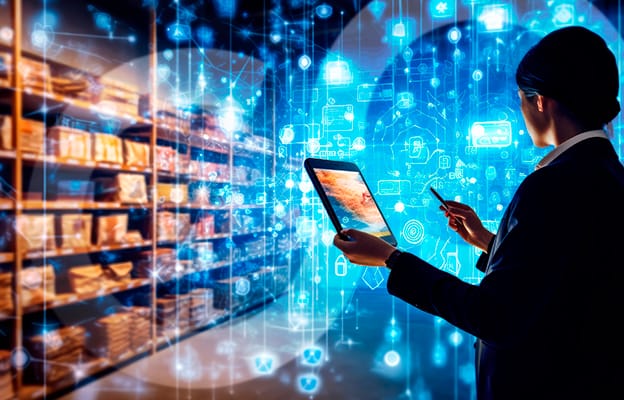
From natural disasters to geopolitical events, these disruptions not only stall the movement of goods but also expose vulnerabilities in efficiency and resilience.
Recent data from the Manufacturing Leadership Council (MLC) claims that 90% of manufacturing executives have faced major disruptions in the past two years that have lead to productivity losses and rising costs.
For industries reliant on complex supply chains, such as manufacturing and retail, these interruptions often result in shortages, delays, and increased pressure to adapt. Even industries like fashion and apparel with more straightforward supply chain can be subject to massive and frequent disruptions.
The COVID-19 pandemic amplified these challenges, shifting consumer demand, increasing costs, and testing the limits of traditional supply chain strategies.
But with disruption comes opportunity: organizations that embrace agile practices, diversify supplier networks, and leverage digital tools can transform their supply chains into resilient systems capable of thriving in uncertainty.
This article explores the nature of supply chain disruptions, their causes, and actionable strategies for mitigating risk—all while considering how businesses can build resilient and adaptive supply chains.
Understanding Supply Chain Disruption
Supply chain disruption refers to unexpected events or conditions that interrupt the smooth flow of goods and services at any point in the supply chain.
These disruptions can stem from natural disasters, geopolitical tensions, labor shortages, cyberattacks, pandemics, or even shifts in consumer demand. As businesses rely on increasingly global and interconnected supply chains, even small disturbances can ripple across industries, causing significant delays, shortages, and cost escalations.
Key Characteristics of Supply Chain Disruption
- Unpredictability: Disruptions often arise without warning, making proactive planning challenging.
- Global Impact: Events in one region, such as a factory shutdown or port delays, can affect supply chains worldwide.
- Cascading Effects: A single disruption, like a shortage of raw materials, can impact manufacturing, transportation, and retail simultaneously
The Economic and Operational Impacts
- Financial Strain: Disruptions can inflate costs, delay production, and reduce profitability. During the pandemic, for example, import prices in the U.S. increased by 13.9% due to supply chain pressures, reported Congressional Research Service.
- Operational Delays: Shipping delays and production halts are among the top concerns for supply chain leaders over the past decade.
- Reputational Damage: Inability to meet customer expectations can erode trust and loyalty, a critical risk in competitive markets.
Modern Solutions (h3)
Addressing these disruptions requires a combination of strategic planning and technological advancements. Techniques like digital twin technology, predictive analytics, and supply chain diversification have proven essential for building resilience and agility in the face of disruption.
This foundational understanding sets the stage for exploring why supply chain disruption matters and how modern tools like Centric PLM™ can help mitigate its effects.
Common Supply Chain Disruptions
Supply chain disruptions are a reality that every organization must navigate.
From natural disasters to geopolitical events, disruptions can ripple through global supply chains, halting production and impacting profitability. Below, we explore the most common causes of supply chain disruptions and their effects, using insights from industry leaders and research.
Natural Disasters
- Examples: Earthquakes, floods, wildfires, and hurricanes can damage facilities and infrastructure, delaying shipments and creating material shortages.
- Impact: For instance, a flood in Europe in 2024 disrupted automotive production, highlighting how localized natural events can have global consequences.
Geopolitical Instability
- Examples: Trade wars, sanctions, and conflicts, such as those impacting semiconductor movement or shipping in volatile regions.
- Impact: Geopolitical tensions can delay or block the transport of critical materials, forcing businesses to scramble for alternative suppliers.
Labor Shortages
- Examples: Worker strikes, pandemic-related absences, and a declining labor force participation rate.
- Impact: Labor shortages during the COVID-19 pandemic significantly delayed manufacturing and transportation. For example, Omicron-driven absences caused severe production delays in early 2022.
Cyberattacks
- Examples: Ransomware and data breaches targeting critical supply chain networks.
- Impact: A single cyberattack can paralyze logistics operations, disrupt schedules, and compromise sensitive data.
Raw Material Shortages
- Examples: Disruptions in mining or agriculture, often exacerbated by geopolitical or environmental factors.
- Impact: Shortages can increase costs and delay production, as seen during the COVID-19 pandemic, which strained global supplies of semiconductors.
Logistics Challenges
- Examples: Port congestions, shipping delays, and last-mile delivery inefficiencies.
- Impact: Increased fuel costs and global transportation bottlenecks led to a 77% rise in shipping expenses from 2021 to 2022, reported EDI Weekly, with significant implications for manufacturers.
Economic Fluctuations
- Examples: Inflationary pressures, currency volatility, and recession risks.
- Impact: Economic shocks amplify supply chain vulnerabilities, often increasing costs and reducing demand predictability.
Pandemics and Health Crises
- Examples: COVID-19 lockdowns, which shifted demand patterns and restricted labor mobility.
- Impact: The pandemic highlighted the fragility of just-in-time supply chains, spurring businesses to explore more resilient models.
Understanding these common causes equips organizations to better anticipate and mitigate disruptions. Modern tools like Centric PLM empower businesses to proactively monitor risks, optimize supplier relationships, and build robust, agile supply chains.
By focusing on resilience, companies can adapt more effectively to these challenges and secure their competitive edge.
How to Better Mitigate Supply Chain Disruption
Supply chain disruptions are an inevitable part of business operations, but they don’t have to be crippling. With the right strategies, organizations can minimize disruptions, reduce risk, and build resilient supply chains that adapt to a rapidly changing world. Below are actionable strategies that leverage modern tools, technology, and forward-thinking practices to manage and mitigate disruptions effectively.
Build Supply Chain Resilience
- Diversify suppliers: Avoid dependency on single suppliers by sourcing from multiple vendors across different regions. In 2024, Garnter reported that 30% of Chief Supply Chain Officers (CSCOs) are shifting to regional supply chains to mitigate risks related to global disruptions.
- Localize production: Prioritize nearshore or onshore manufacturing to reduce risks associated with international shipping and geopolitical instability.
- Invest in redundancy: Maintain buffer inventory or emergency stock for critical components to weather short-term disruptions.
Leverage Predictive Analytics and AI
- Use predictive analytics to forecast potential disruptions, such as natural disasters or geopolitical events, and plan accordingly.
- AI-powered tools can analyze supply chain data in real time, identifying vulnerabilities and optimizing processes to prevent bottlenecks before they happen.
Prioritize Visibility Across the Supply Chain
- Adopt technologies like Internet of Things (IoT) devices and blockchain to track shipments and provide real-time updates on inventory levels.
- End-to-end visibility ensures stakeholders can act quickly in response to delays or unexpected changes.
Strengthen Collaboration with Suppliers and Partners
- Build strong relationships with suppliers by establishing clear communication and mutual trust.
- Conduct joint risk assessments and align on contingency plans to ensure smooth operations during disruptions.
Embrace Digital Transformation
- Adopt PLM solutions: Product lifecycle management (PLM) tools, like those offered by Centric Software, enable teams to centralize data and streamline workflows. This reduces inefficiencies and improves decision-making during disruptions.
- Implement ERP systems: Enterprise Resource Planning systems integrate supply chain operations, providing a single source of truth for planning and execution.
Develop Robust Contingency Plans
- Create detailed risk management frameworks that account for various scenarios, from natural disasters to cyberattacks.
- Test these plans through regular simulations to identify gaps and ensure readiness.
Enhance Workforce Agility
- Cross-train employees to adapt to shifting operational demands during disruptions.
- Use flexible labor strategies, such as remote work, to maintain productivity during crises like pandemics.
Incorporate Sustainability into Supply Chain Strategy
- Develop sustainable sourcing practices to reduce the environmental impact and align with evolving consumer expectations.
- Sustainability initiatives not only mitigate risks but also build brand trust.
Incorporating these strategies helps businesses navigate an unpredictable supply chain environment with greater agility and confidence.
How PLM Can Help Mitigate Supply Chain Disruptions
Supply chain disruptions challenge organizations to be more agile, transparent, and resilient. From raw material shortages to logistical delays, product lifecycle management (PLM) software offers a robust solution to navigate these disruptions.
By centralizing product data, integrating supply chain workflows, and providing real-time analytics, PLM software empowers businesses to adapt and thrive in an unpredictable environment.
Improving Visibility Across the Supply Chain
One of the biggest hurdles during disruptions is a lack of real-time insight. PLM software provides end-to-end transparency by integrating data from suppliers, manufacturers, and logistics partners into a single platform. Key benefits include:
- Tracking inventory and materials: Instantly identify where delays or shortages may arise.
- Monitoring supplier performance: Quickly evaluate and pivot to alternative sources when disruptions occur.
- Streamlining workflows: Optimize production schedules based on real-time supply chain data.
With PLM software, decision-makers have a single source of truth, enabling consistent, informed action across teams.
Driving Agility and Proactive Decision-Making
In times of disruption, speed and adaptability are critical. PLM software enhances decision-making by:
- Enabling scenario planning: Simulate potential disruptions to anticipate their impact and adjust operations proactively.
- Facilitating collaboration: Connect cross-functional teams in real time to align responses and avoid delays.
- Leveraging predictive analytics: Use data-driven insights to identify risks before they escalate.
These capabilities allow businesses to minimize downtime, reduce costs, and ensure continuity even during unexpected challenges.
Integrating Sustainability into Supply Chains
As sustainability becomes a priority, PLM software helps organizations build greener, more responsible supply chains. Key features include:
- Environmental tracking: Monitor the carbon footprint and environmental impact of materials and suppliers.
- Greener sourcing: Identify and prioritize eco-friendly suppliers and practices.
- Waste reduction: Optimize production processes to minimize resource waste and overstocking.
Sustainability not only mitigates risks but also aligns businesses with evolving regulatory requirements and consumer expectations.
How Centric PLM Minimize Disruption Impact
Centric Software’s solutions are purpose-built to address modern supply chain challenges.
Centric PLM provides:
- Real-time collaboration: Seamlessly connect with suppliers, manufacturers, and logistics partners to respond quickly to disruptions.
- Actionable dashboards: Access real-time insights into every stage of the product lifecycle, from design to delivery.
- Supplier management tools: Evaluate and onboard suppliers efficiently, ensuring redundancy and reducing dependency on single sources.
For example, a global fashion brand using Centric PLM reduced its time-to-market by 25% while strengthening supply chain resilience through improved collaboration and data transparency.
By improving visibility, fostering agility, and supporting sustainability, PLM software transforms the way organizations manage supply chain disruptions. Centric PLM takes it a step further with tailored solutions that help businesses turn challenges into opportunities.
Build Resilience Against Supply Chain Disruptions with Centric PLM
For better or worse, supply chain disruptions have the power to derail timelines, inflate costs, and impact customer satisfaction. However, with the right strategies and tools in place, organizations can not only minimize the impact of disruptions, but also turn them into opportunities for growth and innovation.
Centric Software® is purpose-built to help businesses navigate these challenges. By centralizing data, enhancing collaboration, and providing real-time insights, Centric PLM empowers organizations to streamline supply chain operations and optimize product development processes. With features like predictive analytics, supplier management, and scenario planning, Centric PLM equips teams to respond swiftly to disruptions while maintaining agility and control.